The Pulsenics Performance Cataloguer demonstrates high accuracy identifying unfulfillable battery cells during first 12 hours of formation and aging
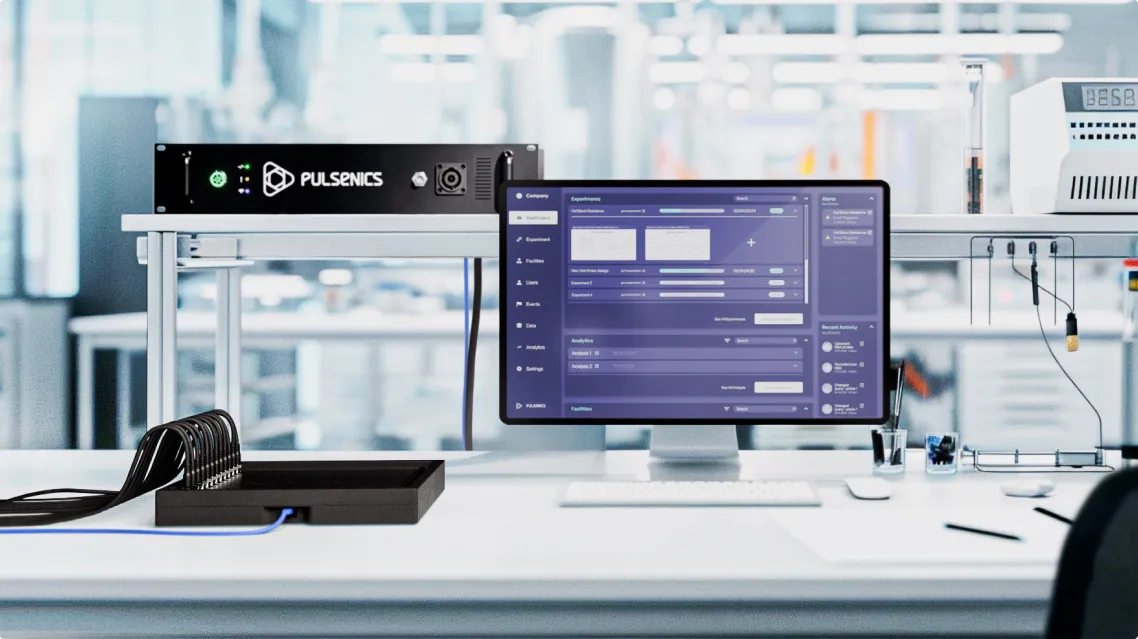
Battery factories have a big problem with unfulfillable cells
Today, lithium-ion manufacturers waste time, money and capacity finishing cells that will ultimately never get through quality control.
These unfulfillable cells — so-called because they cannot fulfill a customer order — are a huge burden on a high-throughput manufacturer.
Unfortunately, manufacturers use the “batch testing” method, where one cell serves as a proxy from a whole batch. This process is expensive, inexact and overlooks outlier cells within batches.
In fact, batch testing can take several months. Each cell can require up to 28 days to complete formation and aging, followed by up to 90 days of cycling.
That’s why Toronto-based electrochemical diagnostics company Pulsenics has launched a revolutionary new solution —The Pulsenics Performance Cataloguer — that combines voluminous data from single-cell EIS testing with the predictive capabilities of AI. Our diagnostics product suite identifies unfulfillable cells within the first twelve hours of formation and aging — over 200x faster than incumbent technologies.
The Pulsenics Performance Cataloguer solves the issue of unfulfillable cells
The Pulsenics Performance Cataloguer saves battery manufacturers money, time and capacity by accurately identifying unfulfillable cells.
Pulsenics levels up EIS for the giga-scale era
EIS has been used widely in academic laboratories for decades. It’s an incredibly powerful technology that can measure impedance in every layer of a battery cell. Experts describe EIS as “opening the black box” of materials because of the depth of insight it provides.
Unfortunately, that same depth of insight has been its biggest flaw. Academic EIS runs single experiments. It’s great for fundamental research, but can’t scan multiple spectra simultaneously or run at high volumes. That has rendered EIS unsuitable for industrial applications.
Until now.
Pulsenics has up-leveled EIS for the giga-scale era. Our in-line, plug-and-play hardware integrates seamlessly into modern battery production and can scale to monitor hundreds of cells simultaneously. Those data streams, run through our proprietary AI model, can rapidly detect defects and predict cell lifetimes with outstanding precision.
Polaris Labs runs a simple experiment
Last year, Pulsenics was engaged by an automotive OEM (Original Equipment Manufacturer) who wanted to know how accurately our solution could identify individual cells that were unfit for market.
Pulsenics engaged Polaris Labs, an independent testing lab in Portland, Oregon, to help us conduct a six-month experiment.
The experiment ran thusly:
- Prior to wetting, scan for mechanical defects
- Validate mechanical defects and discard defective cells
- Send remaining cells into formation and aging, with each cell connected to continuous EIS monitoring
- Continuously feed EIS data through the Pulsenics AI model to produce lifecycle predictions
- Complete formation and aging
- Send finished cells into cyclers and run charge/discharge profiles until end-of-life
- Compare our AI-informed lifecycle predictions with actual outcomes
Although the Pulsenics Performance Cataloguer continuously updated lifecycle predictions throughout the 25-day formation and aging process, all nine cells with short cycle lives were identified within the first twelve hours (2% of the formation and aging timeline). Our model did not flip any lifecycle predictions between fulfillable and unfulfillable after the first twelve hours.
Result: The Pulsenics Performance Cataloguer correctly identified 100% of unfulfillable cells.
Polaris Labs scientists ran the Pulsenics Performance Cataloguer diagnostics on 27 representative lithium-ion battery cells. Of those 27, three had validated mechanical defects and nine had unacceptably short cycle life.
Of the 15 cells identified as market-ready by our AI model, 100% proved to be commercially viable at the end of cycling six months later.
In other words — we called it. 😊
Pulsenics Performance Cataloguer diagnostics on 27 representative lithium-ion battery cells
Test your product exponentially faster with The Pulsenics Performance Cataloguer
The Pulsenics Performance Cataloguer saves battery manufacturers money, time and capacity by accurately identifying unfulfillable cells.
Today, battery manufacturers are wasting unknown millions sending unfulfillable battery cells through formation and aging. These destined-for-scrap products are creating bottlenecks in factory throughput across a low-margin industry where efficiency rules. It’s time for a serious upgrade.
Fortunately, OEMs now have scalable EIS diagnostics to detect defects and predict cycle life at the individual cell level. Pulsenics has solved the bottleneck.
Is the Pulsenics Performance Cataloguer right for your company? Let’s collaborate and find out.
Battery manufacturers who want to validate the offer can rely on Polaris Labs to design, execute and document experiments with maximum transparency. Get quick results you can trust, and start saving millions.
About Pulsenics
Pulsenics leads the field of electrochemical performance diagnostics with groundbreaking hardware, real-time data hub and revolutionary Performance Cataloguer solution. Their novel electrochemical impedance spectroscopy (EIS) solution allows for rapid diagnostics at all volumes. High-throughput OEMs can depend on Pulsenics to forecast cell performance, identify mechanical defects and streamline manufacturing processes with real-time data analysis. Pulsenics is paving the way forward toward a more reliable and efficient electrochemical industry. Learn more at www.pulsenics.com
About Polaris Labs
Polaris, humanity’s celestial North Star, has been used for centuries as a navigational tool to guide explorers to their destination. At Polaris Battery Labs we have the same vision in mind. We are committed to helping battery developers large and small realize the full potential for their products and expedite the path to their destination, commercialization. In addition to our basic cell building services, our highly skilled team offers both technical expertise and marketing savvy based on decades of experience in the battery industry. Learn more at www.polarisbatterylabs.com.